煩雑で属人化した
アナログ生産管理から卒業!

CSCコンサルで
生産管理の課題解決
3万人の人材育成、
2400の改善コンサルティング実績

こんな悩みは
ありませんか?
- 過剰在庫と欠品をなくし、短納期対応できるようになりたい
- 属人化したアナログ管理から脱却して、生産管理のDX化を進めたい
- 管理の精度とスピードを高めて、生産性と利益率を高めたい
- 古い生産管理システムをすぐに更新したい
工程間の連携が困難
自工程優先の管理によって、全体最適が進まず、連携のまずさから納期遅延や品質トラブルが発生。
管理業務の属人化
管理業務の属人化によって、人的トラブルが減らず、管理の標準化やシステム化も阻む。
作業の属人化と人手不足
作業の属人化によって、技能伝承が進まず、能力のバラツキの拡大、人手不足が深刻化。
システムが使いづらい
生産管理システムが生産の実態に合わず、使いづらく、役に立っていない。
CSCコンサルが
解決します。
- 生産管理の構築経験がなくても大丈夫!経験豊富なコンサルがサポートします。
- 新システムの導入前でも問題ありません。デジタル改善ツール付のコンサルです。
- システム開発者がいなくても大丈夫!プロトタイプのシステムはコンサルが提供します。
1.デジタルツール付コンサル
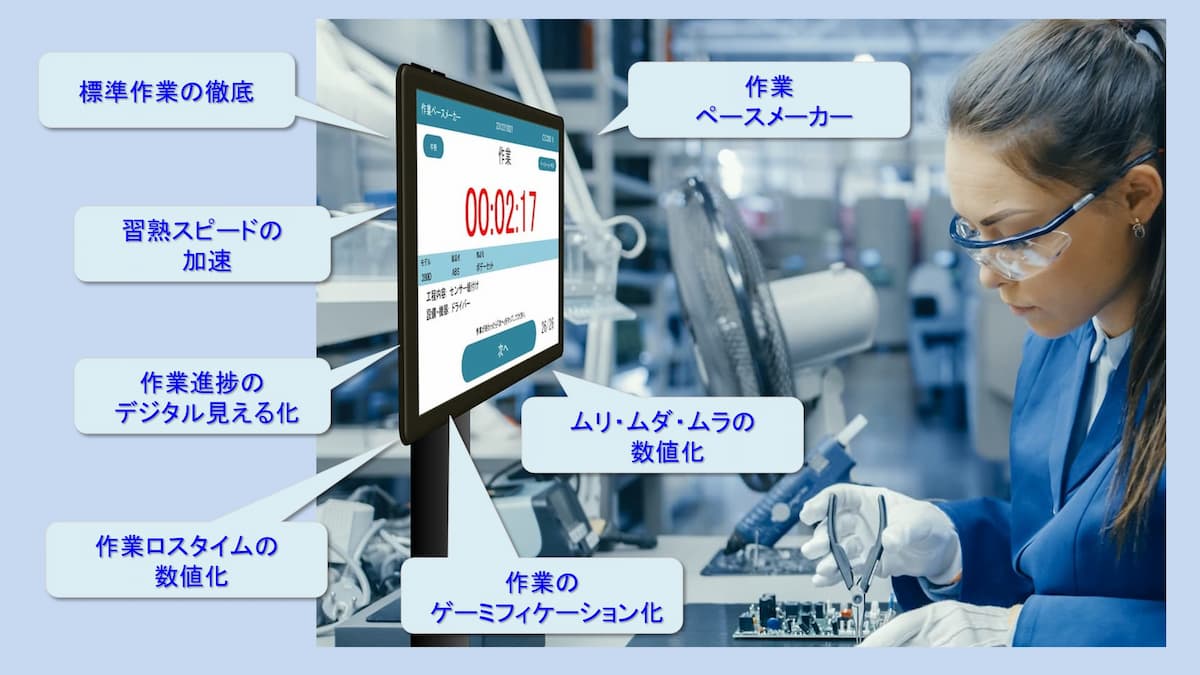
2.プロトタイプで実践知を高める
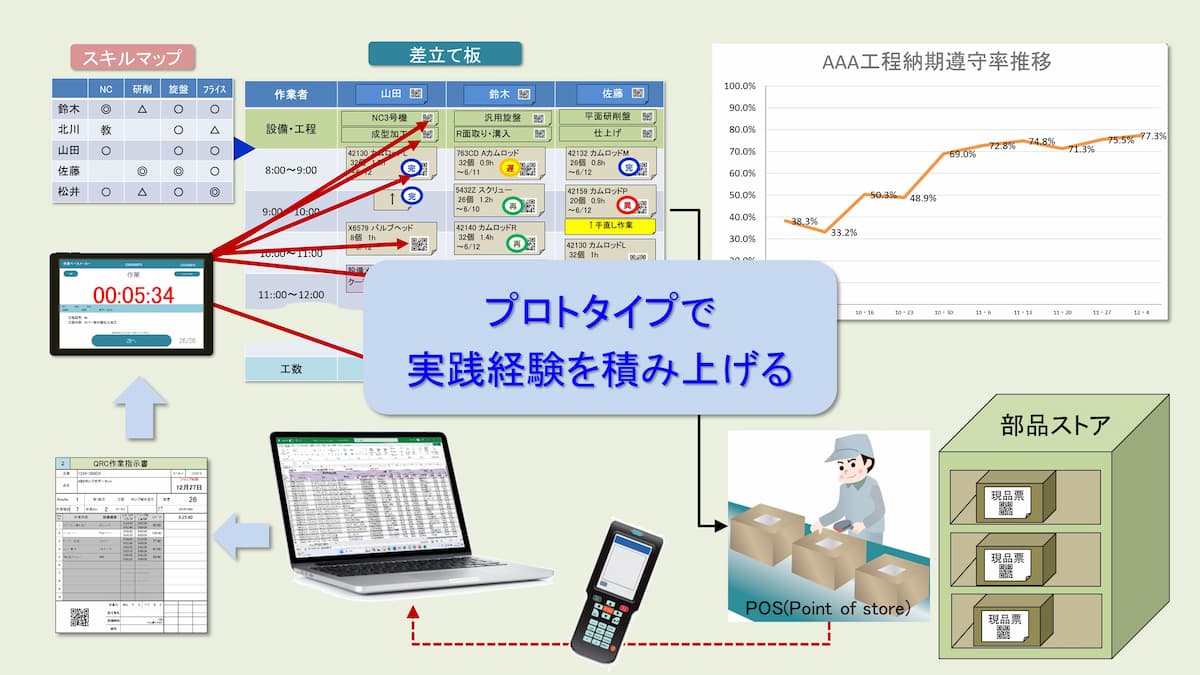
3.トヨタ流コンサルで脱・常識
4.改善をリードする伝道師育成
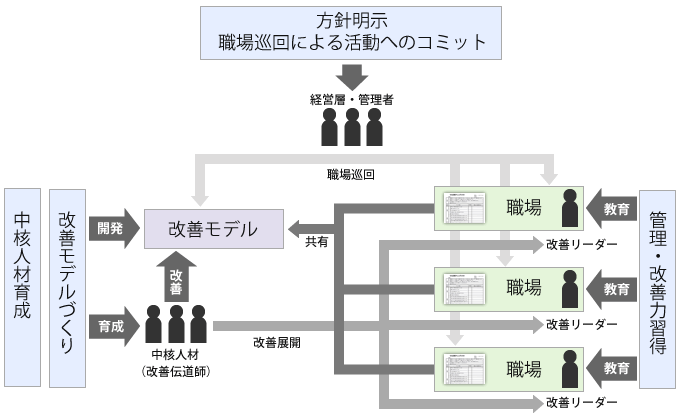
解決事例
- 生産管理の改善でどのような課題が解決でき、効果が得られるでしょうか。生産管理の改善をした企業の事例を紹介します。
【改善事例1】
過剰在庫と欠品の削減
リビング用品を開発・製造・販売するメーカーでは、新製品発表、展示会などのイベント開催、売れ筋商品管理などの情報と季節性の変動を加味した販売予測を立案し、平準化のための在庫を維持する計画生産を行ってきました。
しかし、顧客要求の多様化、ネット販売比率のアップ、コロナ過や為替変動などの環境変化によって、販売予測は外れ、計画生産で積み上げた在庫は消化されず過剰在庫となる一方で、計画外の製品が売れ、欠品となる状況に悩まされてきました。
【実需連動型生産管理の導入】
受注情報に基づく計画数と1週間在庫の組み合わせによる短サイクルローリング生産計画によって、需要変動に追随しながら生産の平準化計画を行う仕組みを構築して、過剰在庫と欠品を削減しました。在庫は、QRコードによる現品管理を導入し、在庫の管理精度を高めることで、在庫量の適正な管理ができるようになりました。1週間サイクルの計画に対応できるように、製造のシングル段取り改善と生産ロットサイズの最小化によって、リードタイムを1週間以下にする改善も並行して行いました。。
【改善事例2】
属人化した管理による日常化したトラブルの解消
輸送機器の部品加工メーカーでは、ベテランの生産管理担当と製造責任者による生産管理を行ってきましたが、顧客からの注文数の変動、短納期化、製造設備のトラブルなどによって、常に生産変更や特急対応に追われていました。
顧客からの要求や設備故障が原因のため、生産管理では対応できない問題と諦めていましたが、同じような生産管理システムを導入している同業他社では、トラブルが少なく、効率的な生産ができているという話を聞き、自社のトラブルの日常化の原因は、属人化した生産管理の問題であることに気づきました。経験や感覚で効率重視の生産計画を維持しようとする管理が注文変動や短納期要求、設備トラブルに対応できず、製造を混乱させる原因となっていました。
【管理ロジックの標準化とシステム化】
受注情報の生産指示展開と実績からの計画修正を行う生産計画と統制限定のプロトタイプ生産管理システムを2ヶ月で作成し、注文変動や短納期対応、設備トラブルを前提した生産管理のロジックと管理ノウハウを実践しながら、作り上げて標準化し、実績からの改善を取り返して、自社に最適な生産管理システムを構築することができ、属人化した管理から脱却することできました。データと仕組みによる管理によって、注文変動や短納期要求にも柔軟に対応できるようになり、設備トラブルへの対処も混乱なくできるようになり、日常化していたトラブルの発生を抑えることができるようになりました。
【改善事例3】
不正確で見えない製造原価を正確に見える化
受注生産の健康食品メーカーでは、正社員、パート社員、アルバイトなど様々な雇用形態の作業者によって製造を行っています。
生産では、注文量の変動によるロットサイズが毎回異なる上に、作業者の経験期間の違いによるスキル差、バラバラの出勤サイクルによるライン編成人数の変動などによって、同一製品であっても作業時間が最大50%以上のバラツキが発生し、製造原価が計算するたびに異なり、正確な製造原価の管理ができないことに悩んでいました。
【作業者一人ひとりの作業の見える化】
作業者一人ひとりにタブレットを配付し、標準作業と時間に対する自分の作業スピードとバラツキを見えるようにして、ペースとリズムをつかませ、工夫できるようにすることで、短期間で習熟度を高めることができました。これにより、ほとんどの人が標準時間通りに作業ができるようになり、作業時間のバラツキを15%以下まで減らすことができ、労務費の算出精度が上がり、正確に製造原価の把握ができるようになりました。配付したタブレットによって、一人ひとりの作業の指示と管理の個別管理ができるようになり、トラブル対応や管理の目が届いていないかった付帯作業などの魑魅魍魎化していた作業内容と時間も正確に把握できるようになり、管理コストの削減改善もできるようになりました。また、様々な作業と時間を正確に把握することで、曖昧であった資材や備品の使用量や共通原価の配賦費も連動して管理できるようになり、原価管理の精度を高めることができるようになりました。
【改善事例4】
古い生産管理システムを最速で更新
設備機器の部品加工を行っているメーカーでは、20年以上前の生産管理システムを使っていました。様々な営業環境や生産状況の変化に対応して、その都度、システムの改修を行い、システムが対応できないことは、各部署が独自の方法で処理していました。
DX化など生産を取り巻く環境が大きく変わってきたため、生産管理システムを更新する計画が立ち上がり、要件定義と処理フロー設計を行っていましたが、1年以上かかっても完了しませんでした。現在の生産管理システムがブラックボックス化している上に、各部署独自の処理が多数あり、それら内容を正確に把握できている人がいないため解析に時間がかかり、各部署の要望を取れ入れていくうちに、複雑で大規模な生産管理システムになってしまったのです。
【リーンスタイルの分散-連携でのシステム導入】
すべてを一度につくるのではなく、生産管理の各機能のプロトタイプを作成し、順に機能拡張していくリーンスタイルで生産管理システムの開発と導入を行いました。最終工程の出荷から遡るように各機能のプロトタイプをエクセルベースで作成し、実務で使いながら必要機能の選択・改善を繰り返し、生産管理システム全体へと広げていきました。着手後2ヶ月で出荷系のプロトタイプでの実践が始まり、半年程度で全工程の生産指示と管理の基本の仕組みが構築できました。各機能を独立したプロトタイプで作成し、連携させる基盤を用意したことによって、各機能に合った既成のアプリなどを適材適所で選択し、組み合わせることもでき、開発期間と費用を抑えることができました。営業システムとの連動など各機能単位で追加変更が自由にできることから、自社に必要なDX化を機能単位で取り入れることができるようになりました。
【改善事例5】全工程が連動する製造のDX化の実現
電子機器の製造を行っているメーカーでは、共通部品が多くあり、注文製品の組み合わせによって各部品の必要数が大きく変わり、各工程の生産数は異なります。また、出勤体制や設備の稼働時間も異なるため、各工程は別々に生産計画を立てて生産していました。
【全工程連動するプロセスチェーンの構築】
工程を連動させる(プロセスチェーン化する)ために、まず、QRコード付き帳票と作業者に配付したタブレットによって工程内のモノと情報と作業(コト)のデジタル化を進め、情報とモノと作業の状態を完全一致させたうえで、デジタル情報を通じて全工程に対する指示と状況把握できるようにしました。工程間の連動は、各工程に設置した部品ストアでモノの出入りを管理するゲート管理と工程別生産管理板の共有によって、負荷の見える化と生産投入順の計画・調整を行い、工程を超えた負荷の平準化とモノのスムーズな流れによるリードタイムの最短化ができるようになりました。プロセスチェーン化は、最終工程から順次、プロトタイプのシステムを作成し導入して、実務に合わせた改善を繰り返しながら広げていき、現場の意識改革とデジタルリテラシーを高めながら進めることできました。
生産管理の
改善コンサルの進め方
生産管理の
課題解決プログラムのステップと内容
Step1 工場診断(生産管理の診断)
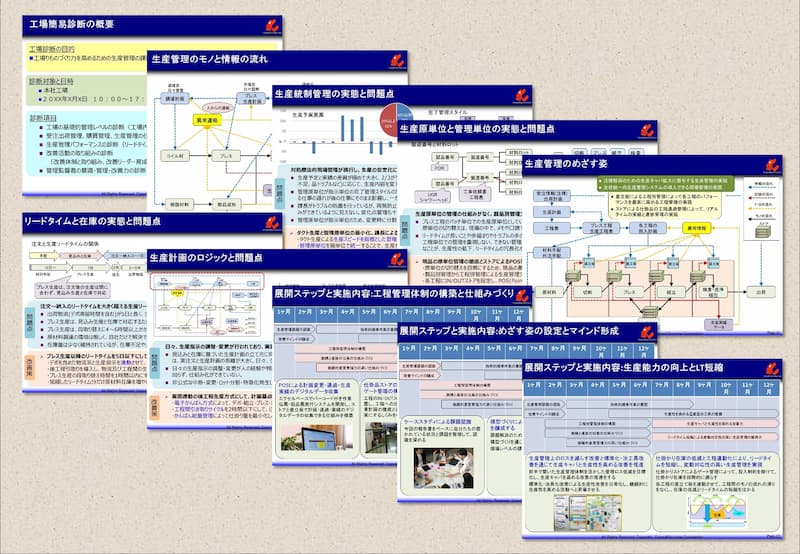
生産管理の課題を洗い出し、改善テーマと取り組み内容を明確にするための工場診断を行います。
改善専門コンサルタントがデータ分析、ヒアリング、現場観察などを行い、多面的かつ客観的に診断・分析を行います。診断結果は、改善テーマと目標、進め方、効果見積もり、体制案、スケジュールなどと合わせて報告及び改善提案としてまとめて提出します。
改善テーマ例(青字:改善方法とポイント紹介)
在庫削減とリードタイム短縮
生産性向上と製造コスト削減
自働化と無人化の推進
歩留り向上と材料費削減
工場DX化対応の現場づくり
作業の標準化と外国人労働者対応
多品種生産体制構築
Step2 推進体制づくり
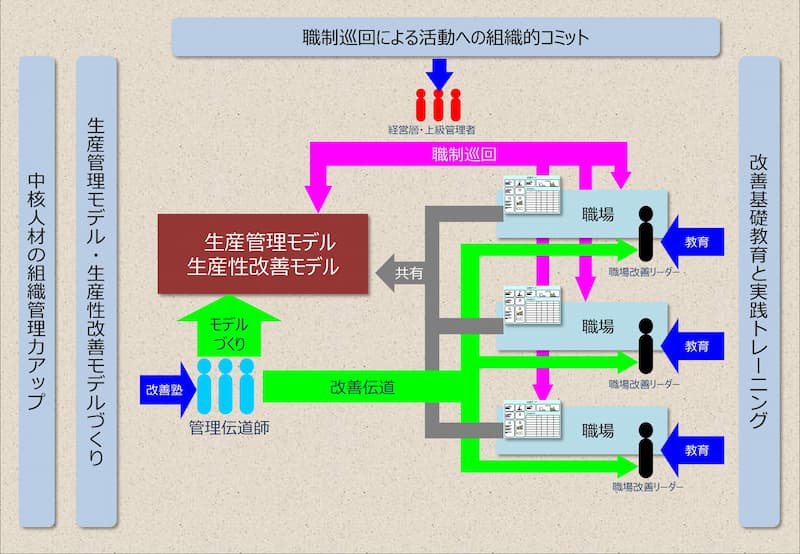
工場診断結果を元に改善を推進する体制づくりを行います。
改善伝道師を育成し、改善に対する抵抗感を払拭し、変えることに対して、前向きに取り組む改善体制をつくります。
経営層・管理者による職場巡回によって、組織的コミットメント体制を築き、水平・垂直の全員参加による一体感と競争意識を高めることで、推進を加速させます。
改善伝道師
改善モデルの見本を示し、ファシリテートすることで、自律的改善を推進する改善の中核となる人材
改善によって組織を進化・成長させる組織管理者のスキルを習得
組織的コミットメント体制
垂直方向の全員参加で、一体的改善行動を引き出す
水平方向の全員参加で、競争意識を形成し、相互に刺激し合い、協業できる改善活動にする
Step3 体験学習型の改善教育
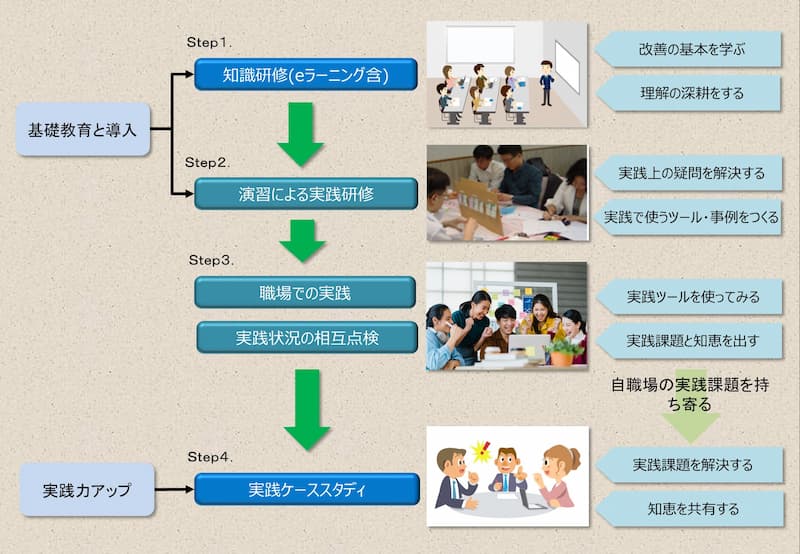
知識教育と実践経験学習、ケーススタディのラーニングミックスによるアクティブラーニング型の改善教育を行います。
貴重なコンサル時間をムダにしないためのオンデマンド動画学習を提供します。
改善を支援する実践ツールの提供と実践経験、ケーススタディによって実践知と力を鍛錬します。
ラーニングミックス
知識で学んだ改善手法などを実践する体験を通じて、改善力を高める体験学習
各自が改善を通じて得た実践知を相互共有して、改善力を相乗的に高める
オンデマンド動画学習
改善に必要な各種手法など400以上の動画学習環境を提供
一人ひとり、必要なタイミングで必要な知識を習得できるのオンデマンド学習
Step4 プロトモデルづくりとシミュレーション
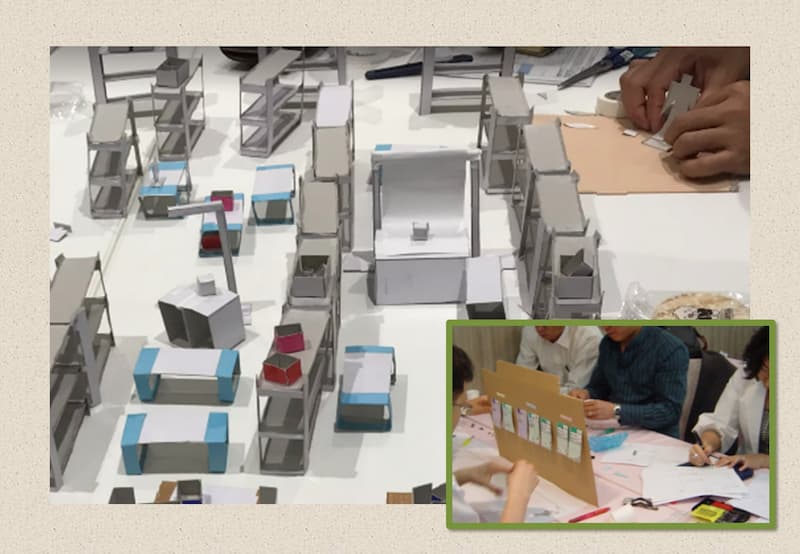
現場の責任者やキーマンの参加による改善後の仮想モデルづくり通じて、めざす姿のイメージを共有し、主体的取り組み姿勢を引き出します。
DCAPシミュレーションによる仮想実施体験を通じて、現場レベルの課題を洗い出し、改善の実行スピードを加速します。
仮想モデル
スケールモデルの模型やデジタル改善ツールによって、改善後の姿をイメージでき、体験できるモデル
自分たちの常識の殻を破り、仕事をパラダイムチェンジさせるモデルづくりをめざす
DCAPシミュレーション
トヨタ流のやってみて考える改善スタイルを仮想モデルでのシミュレーションを通じて実践する方法
仮想実践体験を繰り返し、そこでの失敗経験をフィードバックし、実効性の高い、改善後の姿をつくる
Step5 プロトタイプの作成
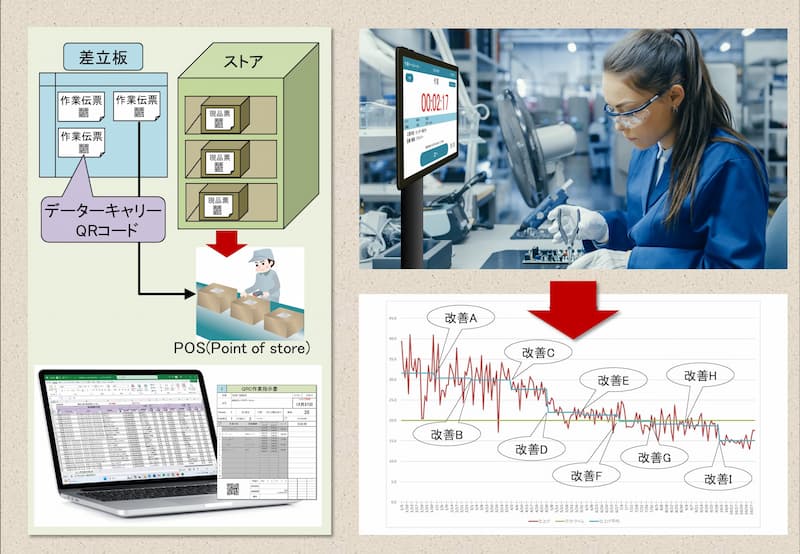
EXCELマクロやVisual Basicベースのデジタル改善ツールでプロトタイプを作成し、システム変更や改修を待たずに、すぐに改善を行います。実践からのフィードバック改善もすぐにできます。(デジタル改善ツールはコンサル費用に含まれます)
デジタル改善ツールでの経験を活かして、DX化に向けた本システムの開発や変更・改修を行うことで、費用が最小にでき、トラブル発生も抑えられます。
デジタル改善ツール例
POS(Point Of Store)
生産工程(ジョブショップ等)に設定するストアにて、モノと情報の連動化(IOT)を行うための改善ツール
DX化に向けた製造実行システム(MES)の基盤となる
データキャリーコード
次システムで必要な情報データを包括したコード
コードによって、データを受け渡していくため、異なるシステム間で情報を共有し、連携して、管理できる
IoTアプリ:ペースメーカー
標準作業の手順と標準時間を徹底し、サイクルタイムが記録できるツール
サイクルタイムのバラツキ分析から、生産性改善を行うことができる
Step6 改善の推進
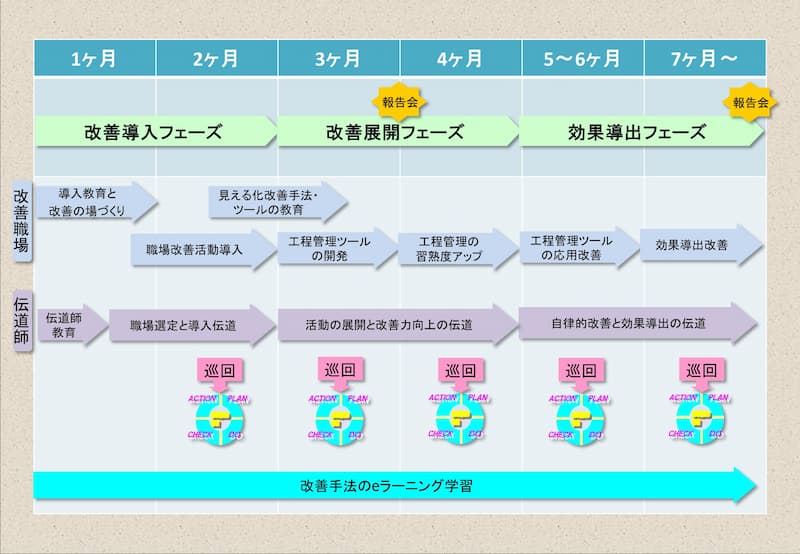
トヨタ流のDCAP改善(やってみて考える改善)スタイルで、職場巡回を行い、現地現物で課題を洗い出し、実践からの学びを活かした改善を行います。
定期なふり返りや報告会で自分たちの取り組み方法を見直し、状況・環境に応じた柔軟な改善を行います。
DCAP改善
トヨタ流のやってみて考える改善スタイルで、実践での失敗経験から学び、改善知を高め続ける改善方法
職場巡回を通じて、経験知を共有し、競争と協業によって、会社全体の改善レベルを高める
ふり返りと報告会
改善職場、改善伝道師、経営陣、コンサルの4者によるふり返りを毎回行い、状況・環境変化に遅滞なく改善をドライブする
中間での報告会で、原点に戻り、改善の合目的性の評価と見直しを行う
Step7 改善進捗の見える化
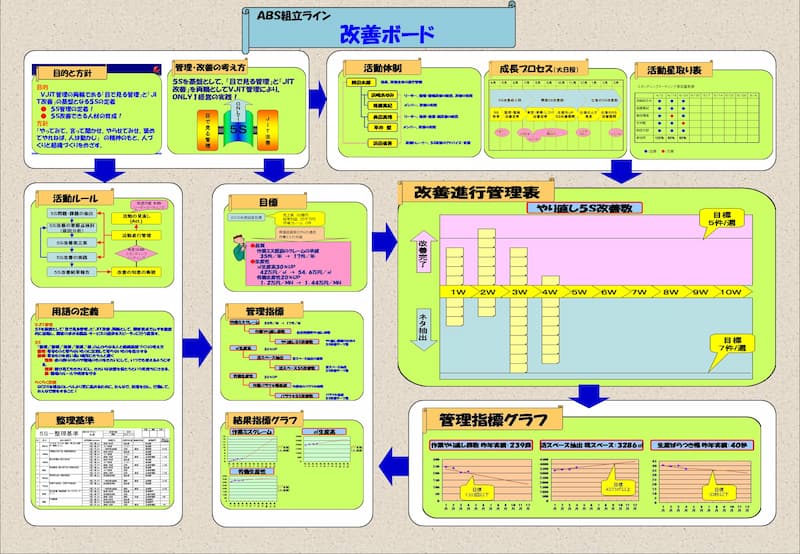
改善ボードによって、改善への取り組みと進捗を見える化し、共有します。
改善活動のベースキャンプとして現場の自律的改善を加速させます。
管理指標によって、改善のレベルアップ度合いを評価し、手ごたえを感じさせることでモチベーションを高めます。
改善ボード
自分たちの改善目的・目標・体制・日程・改善進捗を見える化し、活動のベースキャンプとして現場に設置するボード
改善に対するプライドと競争意識を高めて、改善知を共有し、チーム力を高める
管理指標
目的達成に向けて、改善への取り組みが適切に行われているか評価する指標
管理指標の直近の目標達成をめざす行動を引き出し、手ごたえを感じさせて、モチベーションを高める
Step8 効果のもぎ取り
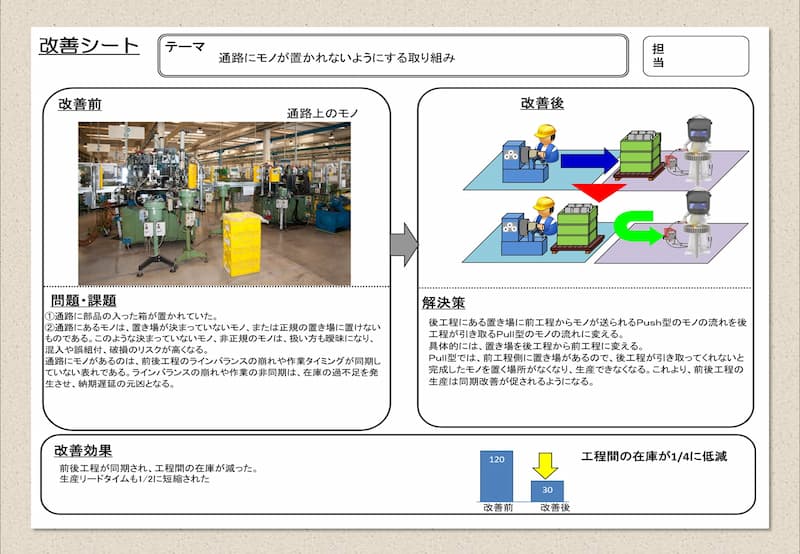
改善効果は、何もしなければ、日々の変動や潜在的アイドル時間などに埋もれて、見えなくなってしまうことがあります。
改善効果を経営レベルの成果として得るために、必要に応じて「改善効果もぎ取りプラン」を立案し、実行します。
例えば、生産性向上では、省人化や時間あたり生産量のアップをはかり、原価低減、利益率アップとしての成果を獲得します。
- コンサルティング及び研修の取引実績
株式会社稲葉製作所
株式会社エネルギア・コミュニケーションズ
カゴメ株式会社
学校法人河合塾
キユーピー株式会社
JOHNAN株式会社
テバ製薬株式会社
凸版印刷株式会社
トヨタ自動車株式会社
富士通株式会社
社会福祉法人福田会
ブラザー工業株式会社
株式会社村田製作所
MIYAO-TOKI(MALAYSIA)SDN.BHD.
公益社団法人愛知労働基準協会
秋田県自治研修所
SMBCコンサルティング株式会社
公益社団法人大阪府工業協会
株式会社オービック
財団法人海外産業人材育成協会(HIDA)
独立行政法人国際協力機構(JICA)
中小企業大学校
東京商工会議所
株式会社ラーニングエージェンシー
デロイト トーマツ コンサルティング合同会社
富山県医師会
名古屋商工会議所
株式会社名古屋銀行
株式会社日本経済新聞社
一般社団法人日本能率協会
独立行政法人日本貿易振興機構(ジェトロ)
株式会社百五総合研究所
碧海信用金庫
みずほ総合研究所株式会社
りそな総合研究所株式会社
Deloitte Kassim Chan(Malaysia)
A.Brain経営コンサルティング株式会社
G-MIC Consulting Inc.
Kakimoto&Nagashima LLP.
KMA Consultants
韓国JMAC株式会社 他
※3万人の人材育成、2400の改善コンサルティング
- 出版実績 >管理改善書籍30冊以上
